Collaborative Robots in a Human-Centered Assembly System- Juniper Publishers
Juniper Publishers- Journal of Robotics
Abstract
This paper offers a brief overview of collaborative
robots and the importance of Design for automated assembly. This means
to not only design the assembly stations with user friendly cobots but
also to analyze and improve the product towards higher physical level of
automation in assembly systems.
Keywords: Collaborative robots; Design for Automated Assembly; Assembly systems; Human-centered
Introduction
Human-centered assembly systems can be describe as a system designed to interact with people intelligently [1].
Collaborative robots is getting more and more common as a solution to
increase the level of automation in production and assembly systems [2]. Case-studies conducted in Sweden shows that over 90 percent of assembly systems still are manual [3],
the cobots could be a solution in order to decrease this percent and to
get more cobots into assembly stations. In cases where the robots are
installed it is more co-existing than collaborative, but there are some
solutions towards a collaborative environment [4-6].
In order to get truly collaborative workstations, the robot and the
operator needs to share both the station and the work piece according to
the standard ISO/TS 15066:2016. Today a lot of the solutions are
technology driven towards cyber physical systems and different virtual
tolls, such as augmented reality. Hence, in order to achieve
collaborative work stations, well designed products for automation is
vital in order to create a well functional collaborative work station.
Design for Automated Assembly (DFAA)
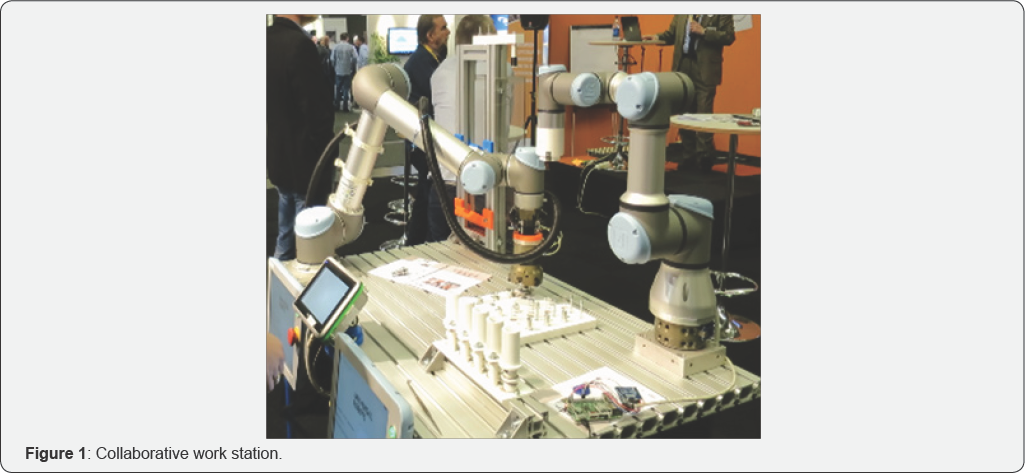
An important step towards an increased level of
physical automation is to design the products for automated stations.
One method is DFA(A), this method was first published over twenty years
ago The idea is to reduce the manufacturing cost such that the design
eases manufacture of the parts making up the complete product without
compromising quality of the final product [7]. Even though, product cost savings between 15% and 70% have resulted from analysis and redesign [8]
using DFA-analysis not many companies uses this method in Sweden. DFAA
provides a clear picture of which components and tasks should be
prioritized to increase automation and could be divided into two main
levels, product level and component level [9]. An industrial case study performed in final assembly aimed to increase automation [6]
also showed a possible improvement of almost 70 percent on the product
level, using DFAA-analysis. The main improvement was to decide a
component to be a main base object and to design fixtures. Fixtures are
very important in order to increase automation in a system [10] and flexible fixturing [11]
can enable an adaptable fixture to be used in a mass customized
systems, which the assembly system often is. The fixtures should be
designed for the main product but also for the components, in order to
be kitted and easily handled by the cobot. On a component level, the
main improvement was also fixturing and sorting of components. A
time-saving of 68 percent per product i.e. 266.8sec ~ 4.5min/product. If
the company produces 10000 products/year = 750h = 18 weeks = 600 000
SEK (if the salary for the operator is 800sek/h). The automated station
illustrated in Figure 1 costs around 500 000 SEK, which means that RoI of this stations is less than 18 weeks.
The assembly fixtures and component fixtures were 3D
printed as a first step. The operator and the robot is sharing the
component fixture, but it is also possible to share the assembly fixture
as well. This means that the station can be defined as a truly
collaborative work station.
Conclusion
In order to increase the usage of cobots in a human-
centered assembly system, the usage of a method such as DFAA needs to be
further developed in order to increase automation in final assembly.
When the allocation between humans and automation is decided,
collaborative work stations can be designed. This paper has presented
some thoughts about the need for a standardization and product design
for automated assembly systems. Cobots is one solution towards an
increase of levels of automation in assembly systems but the product
design might be as important as the safety and user-friendly and
collaborative robots.
For More Open Access Journals Please Click on: Juniper Publishers
Fore More Articles Please Visit: Robotics & Automation Engineering Journal
Comments
Post a Comment