Novel Configurations of Slit Tubular Soft Robotic Actuators and Sensors made with Ionic Polymer Metal Composites (IPMCs)- Juniper Publishers
Juniper Publishers- Journal of Robotics
Abstract
Reported is a new family of ionic polymer metal
composites (IPMCs) actuators, energy harvesters and sensors in slit
cylindrical/tubular configurations. The slit IPMC cylindrical/tubular
elements are made of bending IPMC slit elements distributed
symmetrically around a cylindrical mantle. The slit bending elements
around the cylindrical mantle may be either straight and/or parallel
with the longitudinal axis of the cylinder for linear actuation and
sensing in terms of the length of the entire cylinder or may be
helically wound around the cylindrical mantle to produce a combination
of linear and torsional actuations and even bending for the slit
cylindrical tube. This paper further introduces some models and special
cases of linear IPMC actuators and sensors in slit cylindrical/tubular
form. Experimental results relating the bending deformation to the axial
deformations of slit cylinders are also presented. Of particular
interest is the emergence of undulating linear actuation and sensing by
slit IPMCs and their combination with twisting and bending to create 3-D
soft robotic manipulation and undulation like in an elephant trunk.
Keywords: Novel Configurations; Slit Tubular; Soft Robotic Actuators; Sensors;Ionic Polymer; Metal Composites
Abbrevations: IPMCs: Ionic Polymer Metal Composites; EAPs: Electro Active Polymers
Introduction
Ionic polymer-metal composites (IPMCs) are synthetic
nanocomposite materials. They belong to the family of electro active
polymers (EAPs). IPMCs deform (actuation mode) in an imposed small
electric field (few kV/m). Also, they generate electrical fields
(sensing/energy harvesting mode) upon physical deformation or via
environmental dynamics, like wind or ocean waves (few mVs for small
samples, 10mm x 40mm x 0.2mm). They work both in air and polar liquids
such as water and blood. In both cases the conjugated cations need to be
mobile enough to migrate towards the cathode when an electric field is
imposed on them. This mobility is generally triggered by the osmotic
pressure created by the migration of hydrated cations. The mobility and
reconfiguration of cations can also be initiated if the IPMCs are in or
under water. To maintain consistency in actuation and sensing the IPMCs
may be encapsulated with thin silicone rubber sheath, by spraying them
with silicone spray to maintain a uniform humidity during actuation,
energy harvesting and sensing operations.
An early coverage and review of IPMCs were first
published in 1998 by Shahinpoor, Bar-Cohen, Xue, Simpson and Smith
[1,2]. However, the original idea of ionic polymer actuators and sensors
goes back to 1992-93time frames and the pioneering work of
Osada, Oguro, Kawami, Asaka, Takenaka and Shahinpoor [3-14]. IPMCs are
composed of an ionic polymer like Nafion® or Flemion® whose surfaces are
chemically plated or physically coated with conductors like platinum or
gold. The electrodynamics of charge migration and generation in these
materials are governed by the Poisson-Nernst-Planck field equations
[15-24]. These materials display artificial muscle behavior under an
applied voltage or electric field. For example an applied voltages of 1
to 4 volts for a typical sample of the size 10mm x 40mm x 0.2mm
typically produces spectacular bending (Figure 1).
Ions migration and redistribution, due to the imposed
voltage across a strip of IPMC, result in all kinds of deformations. If
the plated electrodes are arranged in a non-symmetric configuration,
the imposed voltage can induce many kinds of deformations such as
twisting, rolling, turning, twirling, whirling and non-symmetric bending
deformation. Alternatively, if such deformations are physically applied
to an IPMC strip they generate a voltage signal (few millivolts for
typical small samples) as sensors and energy harvesters [25-27].
Figure1a & 1bdepict various deformation
configurations of IPMC strips depending on the placement configuration
of the electrodes chemically plated on the IPMCs. Such twisting/bending
deformations of IPMCs (Figure 1b) may be generated by placing
the electrodes on the IPMC strip in eccentric and non-symmetrical
configurations. These materials generate a force density of about
40 in a cantilever configuration for sizes around 5mm x 30mm x
0.2mm, meaning they can generate a tip blocking force of almost
40 times their own weight in a cantilever mode[12,23]. In other
words if the weight of a cantilever is about 0.06 gmf, based on a
density of 2 gm/cm3, the sample can produce a tip blocking force
of about 2.4 gmf. Figure 2 displays the actuation and sensing
mechanisms in cantilever strips of IPMCs in a graphical manner.
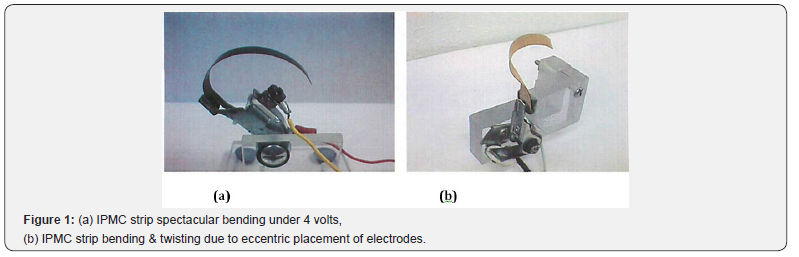
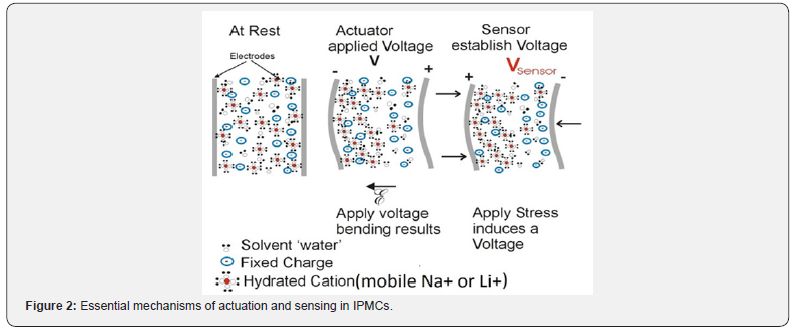
The essential mechanism for both actuation and sensing/
energy harvesting capabilities of IPMCs is the migration of
hydrated cations (Na+, Li+), which are loosely adjoined to the
underlying molecular network with anions, towards the cathode
electrode and away from the anode electrode due to either an
imposed electric field (actuation) or an imposed deformation field
(sensing/energy harvesting). The cations are generally attached to
a number of water molecules (hydration number) which is about
4 for Na+ and 6 for Li+. These deformations are considered to be
related to contraction due to depletion of cations from the anode
side and osmotic pressure or tension due to arrival of hydrated
cations on the cathode electrodes side due to Poisson-Nernst-
Planck phenomena [23,24]. It is expected that for a typical sample
IPMCs in actuation, sensing and energy harvesting modes there
exists a broad bandwidth (kilo HZ and beyond) for their actuation,
energy harvesting and sensing response to an imposed electric
field or deformation field. The migration of hydrated cations
depends on the structure of the base material (DuPont Nafion®,
Asahi Glass Flemion®) and how uniform the electrodes are plated
on the base material.
In the next section, a brief mathematical model for the
actuation and sensing of IPMC is presented.
IPMC Actuation and Sensing Modeling
de Gennes and coworkers [15] presented the first
phenomenological theory for sensing and actuation in ionic
polymer metal composites. Asaka et al. [16] discussed the bending
of polyelectrolyte membrane-platinum composites by electric
stimuli and presented a theory on actuation mechanisms in
IPMC by considering the electro-osmotic drag term in transport
equations. Figure 2 clearly displays the mechanisms of actuation
and sensing of IPMCs. Let us now summarize the underlying principle of the Ionic
polymeric nanocomposites actuation and sensing capabilities,
which can be described by the standard Onsager formulation
using linear irreversible thermodynamics. When static conditions
are imposed, a simple description of mechanoelectric effect is
possible based upon two forms of transport: ion transport (with
a current density, , normal to the material) and solvent transport
(with a flux,Q
, we can assume that this term is water flux). The
conjugate forces include the electric field, and the pressure
gradient
. The resulting equation has the concise form
of
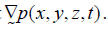

Where,σ and K are the material electric conductance and
the Darcy permeability coefficient, respectively. A cross coefficient
(Onsager’s coefficient) is usually symmetric or 12 21 L = L = L . The
simplicity of the above equations provides a compact view of the
underlying principles of actuation, transduction and sensing of
the ionic polymer nanocomposites. When we measure the direct
effect (actuation mode) we work (ideally) with electrodes which
are impermeable to ion species flux, and thus we have = 0. This
simplifies the equations to:

This
will, in turn, induce a curvature k
proportional to
. The relationships between the
curvature k
and pressure gradient
are fully derived
and described in de Gennes, Okumura, Shahinpoor and Kim [15].
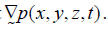
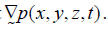
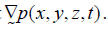
Note that
is the local induced
bending moment and is a function of the imposed electric field
E, Y is the Young’s modulus (elastic stiffness) of the strip which
is a function of the hydration H of the ionic polymer metal
nanocomposite and I is the moment of inertia of the strip. Note
that locally M(E) is related to the pressure gradient such that in a
simplified scalar format [15]:


Note that vectorially the curvature
is related to the imposed
electric field E
Based on this simplified
model the tip bending deflection δmax of an IPMC strip of length lg
can be shown to be almost linearly related to the imposed electric
field. The experimental deformation characteristics of IPMCs are
clearly consistent with the above predictions obtained by the
above linear irreversible thermodynamics formulation which
is also consistent with the above equation in the steady state
conditions. Note also that the value of the Onsager coefficient L
has been estimated to be of the order of 10-8m2/V-s [20-24]. Other
parameters have been experimentally measured to be K~10-
18m2/CP, σ ~1A/mV or S/m. On the other hand one may consider
charge transport modeling of actuation and sensing. The reader is
referred to Bahramzadeh and Shahinpoor [20-24] and Shahinpoor
[22-24] for such Poisson-Nernst-Planck equations. Similar to poly (ethylene-co-methacrylic acid) metal composite, member of
the electroactive polymer can be introduced as biomimetic soft
robotic polymer [28-32].

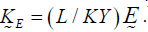
Some Experimental Results
Figures 3(a,b&c) represent experimental results for
deformation (tip displacement and curvature) of a small strip
of slit IPMC (40mm x 12mm x 0.2mm) with simple-supported
ends in a small electric field (under 5 Volts/0.2mm) in horizontal
and vertical directions. For each graph the bestfittedcurve is
constructed to demonstrate the consistency in material response.
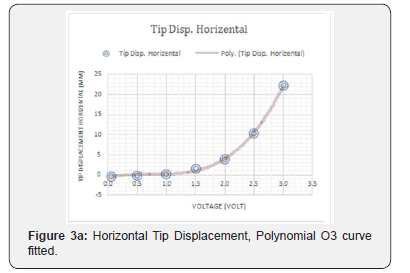
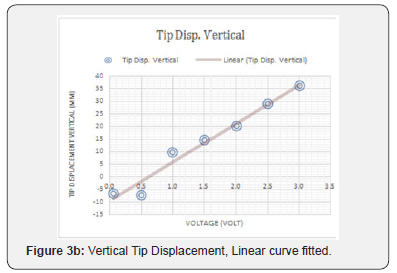
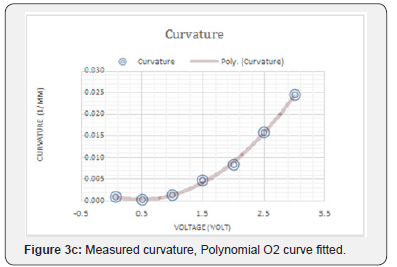
Another set of experimental results were obtained and plotted
in connection with slit IPMC strips with built-in ends to recapture
the tip displacements in vertical and horizontal configurations,
as well as curvature. The results for the second test series are
presented in Figure 4(a,b&c).
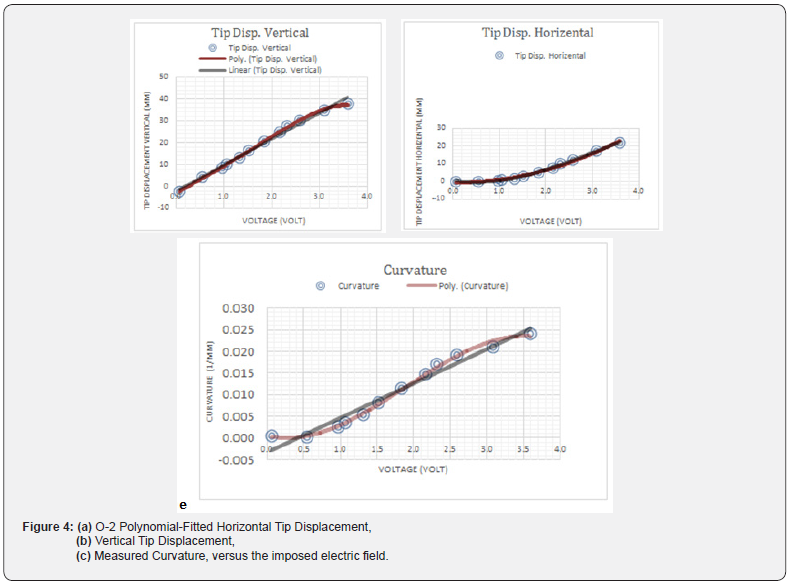
Figure 5(a&b) represents sensing and energy harvesting
characteristics of IPMCs [12,23]. Simultaneous actuation and
sensing of IPMCs are of interest to soft robotic researchers.
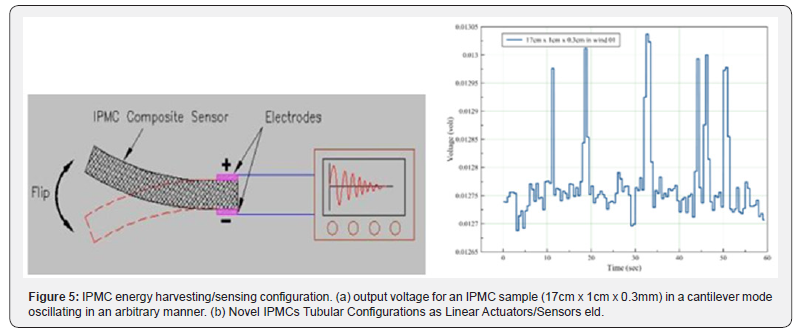
Note that IPMCs havea broad range of applicationsin soft
biomimetic robotic actuation, energy harvesting and sensing
[23-24]. In this section some novel configurations for IPMC
actuators and sensors/energy harvesterswill be introduced.
Based on the reported test results in Figure 3&4 for large
deformation and actuation of IPMC materials, it is expected these
novel configurations will be practically useful for engineering
applications.Asimpledescription of actuation in this type of
material is based on cationic migration towards the cathode to
expand the cathode side of IPMC by osmotic pressure and contract
the anode side of the IPMC resulting in bending towards the anode
side as depicted in Figure 2.
In other cases and configurations, the IPMC sample can be
considered as a non-slit cylinder/tube such that it can act like a
linear actuator and generate an axial force (Figure 6).

In the sensing mode, the axial forces on both ends force
the cylinder to shrink and thus, as a result, the material will
accommodate the deformation. This accommodation can be inward
or outward. The pressure gradient due to this accommodation
will generate the expected signal to sense the displacement [12].
Regarding the buckling instability under axial loading, the non-slit
cylindrical/tubular structures will have initial slight curvature
outward or inward to minimize buckling instabilities. In addition,
from actuation point of view, an applied electric field causes the
non-slit cylinder/tube to contract/expand axially/laterally as
shown in Figure 6, based on the voltage polarity. This applied field
will gradually deform the cylinder to become more like a sphere
(Figure 6d).
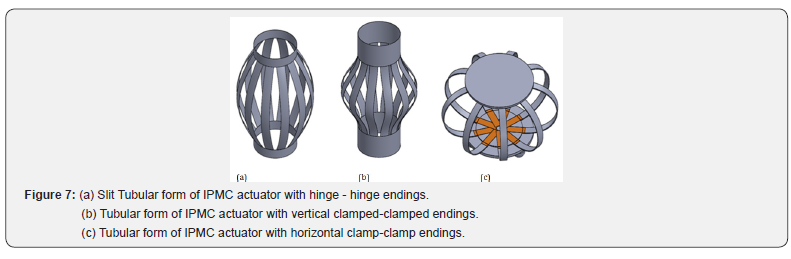
Another case will be using IPMC strips around a cylindrical/
tubular object or a slit tubular IPMC. Some of the configurations
of slit IPMC strips around a cylindrical/tubular mantle are shown
below in Figure 7(a,b&c).
In the slit tubular configurations in Figure 7, slit IPMC
cylindrical strips experience two major forms of boundary
condition for this type of the actuator/sensor family (Hinged in
Figure 8a and clamped in Figure 7(b&c). Other form of boundary
condition will provide more complex manipulation and maneuver
possibilities that will be discussed later. These concept also are
likely to be used for applications in pumps/micro-pumps in which
the pushing or taking in a fluid can be performed by bending/
deformation of the slit strips in which an inner housing should
accompany the assembly. In other word the volume change due to
the movement of the IPMCs will initiate the pumping action.
Regarding the sensing mode, whenfor the slit IPMC strips are
in a hinge-hinge or simply-supported configuration, there will be
less force requirement for the desired displacement andit further
results in generatinghigher output voltage. Further, during sensing
action the effective length of the IPMC strip is longer. Figure 8,
demonstrate the curvature variations related to this formation
such that the red regions are in compression and green regions
are in tension and the green parts are almost straight.
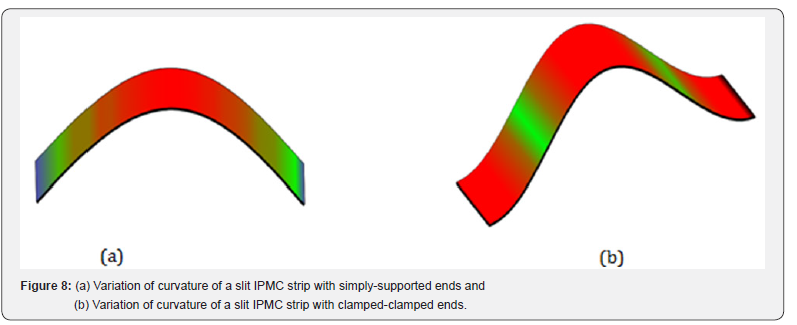
It is also reasonable to note that due to having longer effective
length, the hinged-hinged model will have a larger force capacity
in actuation. The model with clamped ending will have a shorter
effective length to generate output signal and requires a higher
level of voltage to operate.
Figure 9 depict a simple form of slit IPMC cylinders in straight
simple pinned ending format (Figure 10).
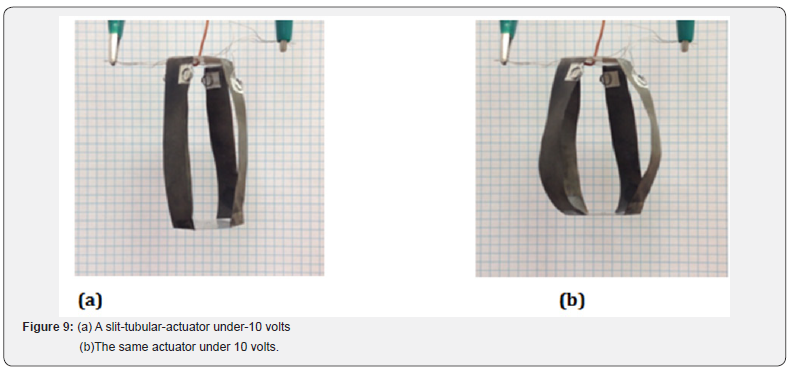
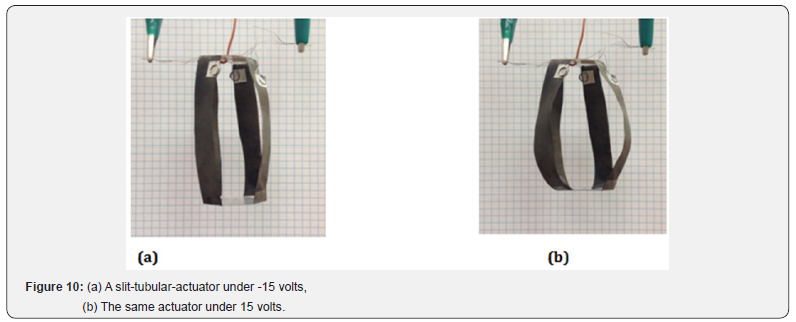
Some variations of these slit cylindrical configurations have
been introduced previously by Yeom and Oh [30], Kamamichi [31]
and Shahinpoor [23,24] in connection with jellyfish swimming
and multi-fingered soft robotic grippers, Figure 11.
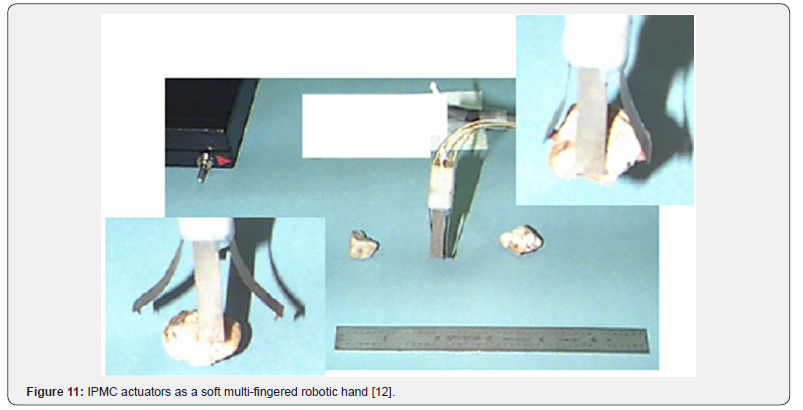
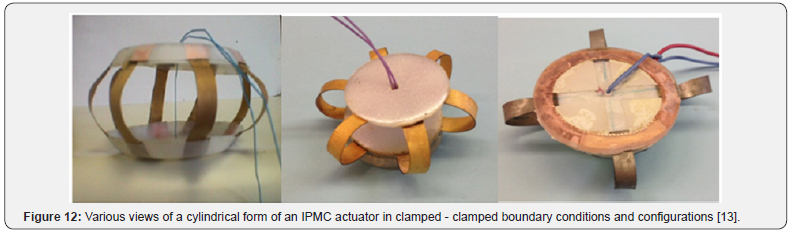
In case of attaching the platform to an arm, these legs can act
like multi-fingered soft biomimetic robotic grippers to grasp and
manipulate objects.Other configurationswere also discussed by
Shahinpoor and Kwang [13], as shown in Figure12
The hinged-hinged configuration will help this possibility in
a more efficient way to have longer actuation range.The bending
for sensing is generally outward rather than inward because the
slit IPMC strips considered are initially slightly bent outward to
prevent any buckling instability.
From another point of views, slits on cylindrical configuration
can be at an angle to introduce the helically twist and sloped
version of helical form of IPMC shown in Figures 13(a&b). This
configuration of helically slit IPMC strips will generate axial and
twisting motion upon actuation and yet it produces electricity
once axially squeezed. Here since the twisting and retracting are
related to each other, the model is considered to be more like an
actuator.
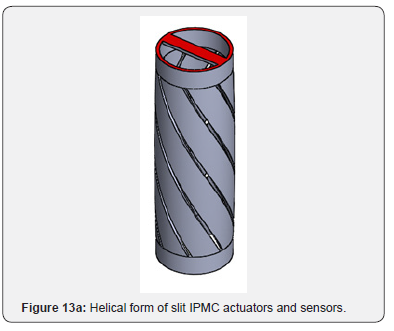
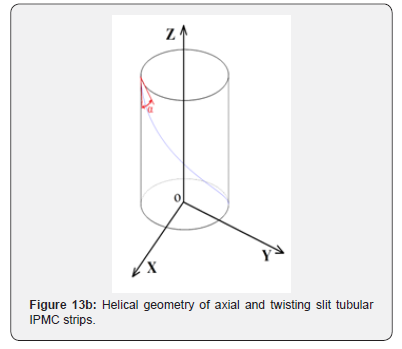
These configurations of slit IPMC strips produces twisting and
linearly moving actuators similar to an automated drill/screw
driver. Note that the helical IPMC actuator/sensor slit strips are like
space curves with coordinates x, y and z such that x = r cosϕ y = r sinϕ and z = c ϕ for ϕ[0,2π] 2π ]where r is the radius of
the helix and c is a constant giving the vertical separation of the
helix’s loops and ϕ is an independent parameter. The tan α= c/r
is slop of the strip sample. The curvature of the helix is given by
torsion
of a helix is given by 


Some studies and modeling for the types of combined linear/
twisting actuators reported in this paper have been proposed by
Li and Kim [32] and Moeinkhah and Rezaeepazhand [33] and
others. Figure 14(a, b&c) depictvarious configurations of helical
assembly of slit tubular IPMCs for actuation, energy harvesting
and sensing with more geometric complexitiesare currently under
investigations and will be reported later
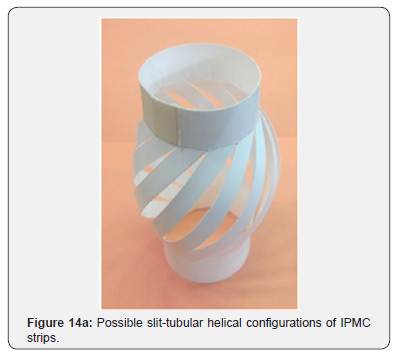
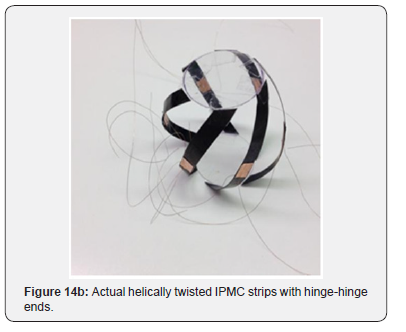
Soft Robotics Snake-Like Configurations Based on Linear-Torsional IPMC Actuators/sensors
Here the initial form of the device considered for the
tubularactuators/sensors is a combination of axial and rotary
movements that resembles slithering snakes,as shown in Figure
15 below:
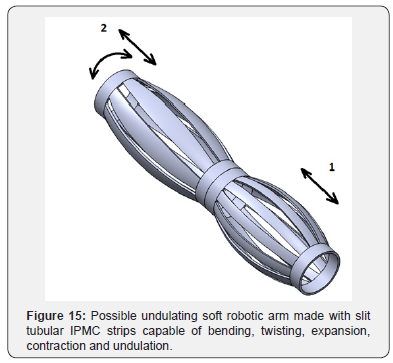
In Figure 15 note that by a combination of movements 1 and 2,
the device is capable of 3-D undulating anobject like an elephant
trunk or a slithering snake-like flexible robotic manipulator [30].
Referring to Figure 16, in case of having more combination of these
actuations configuration, possibility of having a more complex
robot can be expected as it is depicted in Figure 16
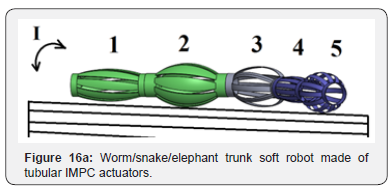
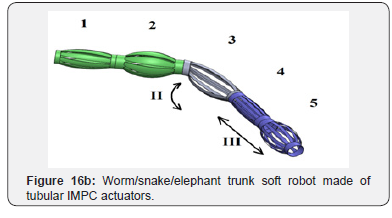
In Figure16 (a&b) a variety of control and boundary condition
can be applied to the assembly to move the soft snake-like, wormlike
or elephant trunk-like soft robots. For the rotary movement
in the direction denoted by I, actuators 1 and 2 are helically
arrangedand can produce a combined rotation and slithering
movement. The actuator number 3 in Figure 16b enables bending
and twisting due to having unsymmetrically applied voltages to
generatehelical and planar movements in the direction denoted
by II. Yet extensional movements can be achieved by actuator 3
in Figure 16b in the direction denoted by III. Thus, we conclude
that combination of cylindrically and helically arranged IPMC
actuators are capable of generating elephant-trunk like motion.
Conclusion
A new family of IPMC linear actuators and sensors in the form
of a slit tubular structure was introduced and discussed. These
groups of actuator and sensors were considered to be made with
bending/twisting slitIPMC elements symmetrically distributed
around a cylindrical/tubular mantle. These types of soft actuators
and sensors are capable of generating a combination of actuation,
energy harvesting and sensing consisting of linear expansion,
contraction, bending, twisting and rotating action similar to a
slithering snake or an elephant trunk.Theslit bending elements
around the tubular mantle were designed to be straight and parallel
with the longitudinal axis of the cylinder for pure linear actuation
and sensing in terms of the length of the entire cylinder. However,
the possibility of helically winding the bending elements around
the cylindrical mantle to produce a combination of linear and
torsional actuation and bending for the cylinder was also briefly
discussed. This introduction of linear/torsional actuation/energy
harvesting and sensing opens the possibility for introducing new
family of soft biomimetic robotic actuators and sensors. The
next steps in development of advanced elephant-trunk-like soft
biomimetic robotic actuators and sensors are to further explore
various cylindrically and helically arranged IPMC strips. Currently,
we are further exploring such possibilities towards fabrication an
elephant-trunk type soft robot.
For More Open Access Journals Please Click on: Juniper Publishers
Fore More Articles Please Visit: Robotics & Automation Engineering Journal
Comments
Post a Comment