Modelling and Simulation of AGVs Using Petri Nets- Juniper Publishers
Juniper Publishers- Journal of Robotics
Introduction
It is a technologically anticipated development that
robotics in our age will become widespread and find common application
areas in almost all sectors such as defense, transportation, health,
service and manufacturing. This process is still expanding and the role
of robots in everyday life as well as in industrial applications is
increasing. One of the important applications of robotic systems in
manufacturing environments is automated guided vehicles (AGVs). AGVs are
autonomous systems controlled by a central control unit, operate
autonomously without the need for an operator, and are used for
transporting materials from one point to another [1-3]. An AGV reduces
the number of occupational accidents that occur due to human beings
because it fulfills all kinds of transportation operations without human
interference in departments such as production, logistics, warehouse
and distribution. These systems, which are used to transport all kinds
of goods in industrial environments, are one of the most suitable
systems to reduce costs and increase productivity. The AGVs can see the
obstacles in their way due to the highest level of security measures
used and sensors, slow down and stay at a safe distance. So, they can
work safely in the same environment with people. Because of all these
features and modularity, AGVs are frequently used in modern and flexible
manufacturing systems today.
AGVs carrying products/parts/materials between
workstations are controlled by their own (embedded) computers/processors
and they are connected to the central computer. The design and
operation of AGVs, which are quite complex and expensive systems, are of
great importance for achieving high performance in their use. AGVs,
which are finding increasingly more application areas and capable of
carrying tasks at different scales in various environments, are today’s
one of the major mobile robotic systems. For this reason, modeling and
simulation of behavior of AGVs in working environments is of great
importance and one of the most powerful tools for behavioral modeling of
AGVs is Petri nets. Petri net is a bi-partite mathematical and
graphical formalism consisting of place, transitions and arc as main
constructs. Generally, places
represent resources, transitions transformations and tokens holding of
conditions, but any concept can be assigned to constructs depending upon
modelling approach. Petri net can be used to model discrete event
dynamical systems (DEDS) [4-8]. Petri net has the capability to model
and analyze a discrete event dynamical system (DEDS) and an AGV embedded
in a flexible manufacturing system is a good candidate to qualify for
implementation of Petri net method. This paper summarizes two research
studies for modelling, simulation and analysis of AGV behaviors using
Petri nets. One of them is a Petri net model for the intended behavior
of a demonstrative AGV for transferring packs between stations in a
pre-defined manufacturing environment. The second is a Coloured Petri
net model of a loop layout automated guided vehicle system embedded in
an automated manufacturing system.
Petri Net Based Behavioural Simulation of a Pick Packing AGV
Petri net is used in our behavioural modelling and
simulation study for a demonstrative pick packing AGV as an
implementation of systematic behaviour-based design approach [9]. The
AGV is considered as required to transfer some packs between four
stations in a pre-defined environment. A Petri Net model for the
intended behaviour with three pre-specified missions is developed based
on rough conceptual structuring of the AGV. Model development and
simulation has been done successfully using Artifex modelling and
simulation environment [10,11].
The general design requirement in the present case
study is considered as the conceptualization of an AGV model to transfer
some packs between finite number of stations and therefore, the
required system is called as a “pick packing AGV”. The operational
behaviour of the pick packing AGV is based on a scenario and it is
described as follows: The AGV will be able to travel in a predefined
physical environment between a “Start Point” and four stations, and to
transfer some packs between these stations. The AGV is expected to
accomplish predefined missions without any external interference. A
Petri Net model used to represent and simulate the intended behaviour of
the
pick packing AGV. The model is developed using ArtifexTM
Graphical Modelling and Simulation Environment which a
C-based development platform for discrete event simulation.
Figure 1 shows the Top-Level Behavioural Model of the AGV in
the ArtifexTM environment. The Top-Level Behavioural Model
consists of six objects, namely units, which are Power Source
and Processor Units, Right and Left Wheel Units, Robot Arm
Unit and Gripper Unit. All units are connected to each other by
interconnecting links that models the communication between
these units. Petri Net structure of each unit is embedded in the
top-level model.
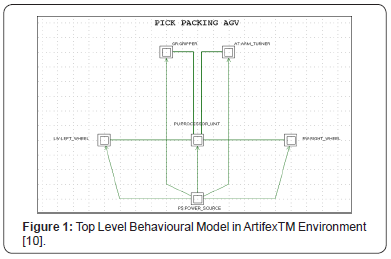
Modelling and Analysis of AGV for an Automated Manufacturing System using Coloured Petri Nets
A loop layout automated guided vehicle system embedded
in an automated manufacturing system has been modelled
and analyzed by applying colored Petri net method. This study
focused at developing of automated guided vehicle system
for serving a flexible manufacturing system comprising of
six workstations arranged in a loop layout. AGVs are serving
workstations moving sequentially in a loop layout. AGVS
has been modelled and analyzed using Petri net method,
specifically using color Petri net class implemented by CPN
Tools. Modelling and analysis have been extended in this
study by developing a lab scale prototype of an AGV which
has been experimentally tested and verified in an automated
manufacturing system. Simulation experiment results have
been validated by developing and employing an AGV prototype
inside an automated manufacturing system. The results
show that an increase in number of AGVs in an automated
manufacturing system increases system throughput whereas
an increase in AGV speed, for a fixed number of AGVs in the
system, is causing a decrease in throughput. The approach
developed in this study can be employed to different system
configurations to determine system performance.
Conclusion
As AGV systems find more application areas in industry,
their modelling and simulation becomes more significant for
industrial system design. Petri net tools are practical and
highly useful tools to study and develop model design before
expensive implementation. It is highly versatile at moderate
sophistication and reasonably reliable output. A physical
prototyping after modelling and simulation would be highly
useful to foresee any probable problem location within the
system before full scale testing. It is also a highly efficient
approach for educational purposes at graduate levels.
For More Open Access Journals Please Click on: Juniper Publishers
Fore More Articles Please Visit: Robotics & Automation Engineering Journal
Comments
Post a Comment