Geometric Simulation for 3D-Printed Soft Robots- Juniper Publishers
Juniper Publishers- Journal of Robotics
Introduction
Robots fabricated by soft materials can provide
higher flexibility and thus better safety while interacting with natural
objects with low stiffness such as food and human beings. With the
growth of three-dimensional (3D) printing, it is even possible to
directly fabricate soft robots [1,2] with complex structures and
multiple materials realizing highly dexterous tasks like
human-interactive grasping and confined area detection [3]. However,
with such increased degrees of freedom (DoF), the design of soft robots
becomes a very difficult task. It can be made possible by integrating
simulation into the design phase. However, the shape deformation comes
from many different and complex factors including manufacturing process,
material properties, actuation, etc. Especially with the limited
understanding of layer-based additive process in AM, it is challenging
to formulate a complete mathematical model for the simulation.
SOFA [4] is one of the most widely used frameworks
for physical simulation. It is also applied in the simulation of soft
robots that supports interactive deformation [5]. However, it may suffer
from the problem of numerical accuracy, particularly
if there is large deformation. Unfortunately, one benefit of soft robot
is its capability of adapting to highly curved contact by large
deformation, which needs to be precisely simulated for many
applications. There is another type of simulation methodology to
simplify the simulation model of deformation to a geometry optimization
problem [6]. It was originally developed in the computer graphics area
for visualization, but it has been proved to work superbly in physical
simulation like self-transformation structures [7] and the computational
efficiency is remarkable [8]. This geometric simulation is particularly
suitable for soft robots [9] (Figure 1), because the actuation of soft
robots is commonly defined by geometry variations (e.g., cable
shortening and pneumatic expansion), and it is actually indirect to
first obtain apply them in the conventional deformation simulation. It
is shown that the geometric simulation gives better convergence and
accuracy than the conventional methods. Therefore, the aim of this
review is to share this technique with a broader audience in the robotic
community, and discuss the potentials capabilities, and future works of
this technology.

Geometric Simulation
The common way of Finite Element Analysis (FEA) is to apply
Hooke’s law to each element and then assemble the equations to compute the deformation with the applied force:

where 𝐹 is the global nodal force vector, 𝐾 is
the global stiffness matrix, and 𝛷 is the global nodal displacement
vector. In the geometric simulation, the formulation is developed by
shape projection on the elements in terms of point positions:
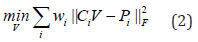
where 𝐕 ∈ ℛ𝑛×3 stacks all the point positions of
𝑛 vertices, Ci ∈
ℛ𝑒×𝑛 is the centering matrix for the 𝑖-th element among 𝑒 elements,
Pi ∈ ℛ 𝑒×3 is the variables defining the shape projections for the
element, and 𝑤𝑖 is the weight for the element, which is commonly
set as the volume. This minimization can be solved by taking
derivative and thus a sparse symmetric positive definite system:

This geometric optimization is formulated to minimize the
elastic energy with reference to shape variations similar to the
physical phenomenon during deformation. To compare Eq. (3)
with Eq. (1), they have the same form with:

Therefore, the geometric simulation actually has the
benefits
as the FEA, but it should be noted the force vector 𝐹 here is defined
purely by the shape projections. As a result, this is a direct
approach to take the geometric actuation as input and compute
the deformed shape of soft robots by numerical optimization using
a geometry-based algorithm. To complete the formulation, the
shape projections should be carefully defined to model different
actuations in the simulation and to model the material properties
geometrically. In the state-of-the-art work [9], the geometric
constraints of actuations are modeled as a type of element, e.g.,
aligning the cable with the edge of elements and shorten the edges,
or scaling the size of elements for volume expansion in pneumatic
actuations. In such way, the actuation can be directly integrated in
the optimization without additional
computation burdens. In terms of modeling the material
properties geometrically in the framework, a calibration step is
done to learn the relationship between material properties and
shape parameters between hard and soft assignments. Should the
element be rigid or preserve its volume is determined by the shape
parameters and modeled by the shape projection. It is shown that
the calibration method can be used to simulate the deformation
of objects with two materials. Different from using constrained
nonlinear optimization, the geometry optimization can converge
in a few iterations, thanks to the shape projection operator.
Discussion
The development of geometric simulation was motivated
by the observation that most actuations of soft robots such as
length shortening of cable and volume changing of chamber
are based on geometry variation. The geometric optimization
tries to preserve shape during deformation with the function of
representing actuations as different type of geometric constraints
to be imposed on specially designed elements. It shows promising
results in terms of accuracy and efficiency, and it is also shown to
be possible in the dynamic models [10].
Conclusion
The preliminary results of the geometry-based framework
are attractive, and its efficiency opens the opportunity of iterative
design for soft robot. However, the current development is
still limited with simple structures, materials, and actuations.
Therefore, to make this simulation more practical and user
friendly, the future works should include extending to different
actuations such as thermo, magnetism or electro ones; multiple
actuations acting together; multiple materials; non-linear material
like hyperplastic material [11]; and multiple bodies with collision
detections.
Comments
Post a Comment